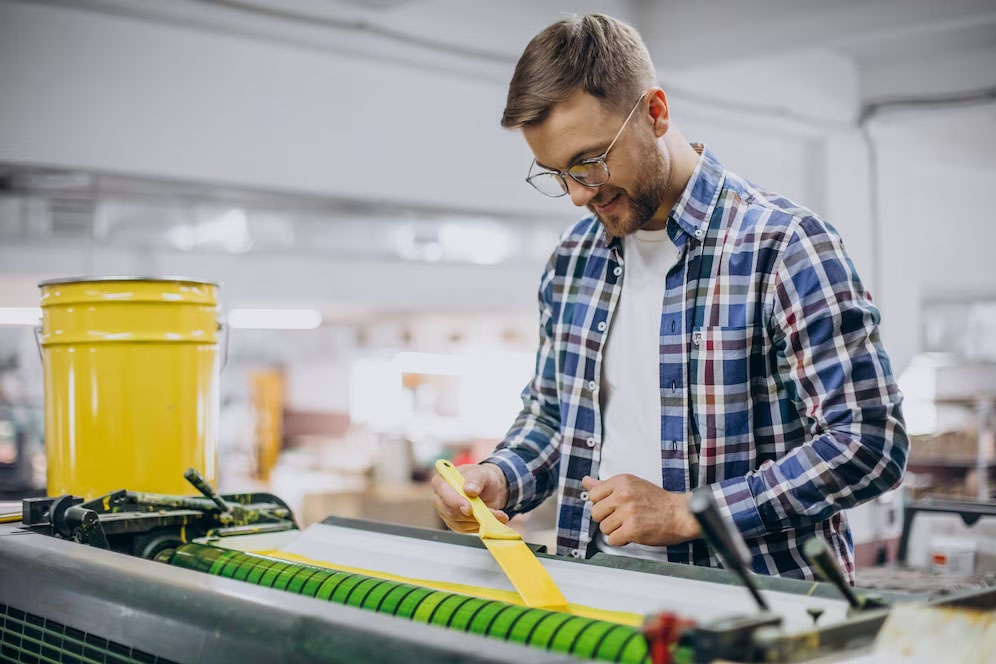
Screen Printing All Over
Printing is the simplest and most straightforward way to get your designs onto a garment, but it has limits when you go to a regular clothes manufacturer. Movemad International has you covered with its customised cut and sew services as well. When you order personalised apparel from us, we do not print on pre-made garments. Instead, we provide cut panels for printing, so you don’t have to worry if you have spots that other clothing manufacturers told you were unattainable or impossible to execute. We’ve got you covered if you’re having issue with white marks on sublimation. We’ve got you covered if you’re having problems with all-over screen printing. If you’re having problems putting your logo on the edge of one sleeve or printing in unusual placements, we’ve got you covered. We have you covered if you want to put a distinctive pattern on your hoodie pocket and make it stand out from the rest of the product. If you are having problems with print positioning, Movemad International will discover a suitable solution for you and will never say no to any form of customisation. Silk screen printing, all-over sublimation printing, heat transfer printing, digital printing, and even direct-to-garment printing are all available from Movemad International.
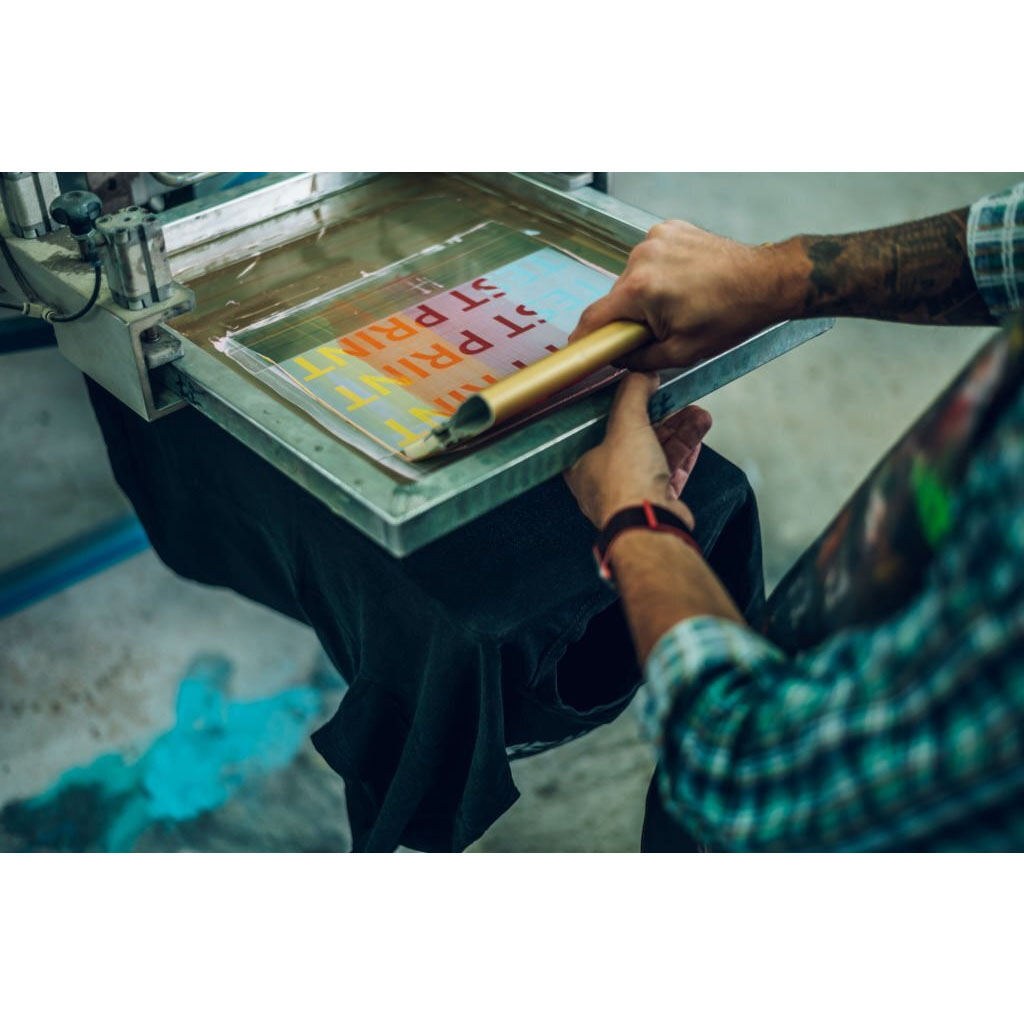
Screen printing on silk
Silkscreen printing is one of the most common and simple methods of imprinting designs on a product. Because of its fabric-friendliness, it can print solid-color graphics on nearly any fabric, regardless of blend or processing. Movemad International employs negatives instead of butter paper for the majority of the complicated designs, resulting in a sharper and clearer image. Because we do not use current machinery for difficult designs, the best element of our screen printing process is our capacity to do complex designs at any place. As a result, the best output is produced, with maximum customisation in terms of print positioning and matching the needed colours of any design.
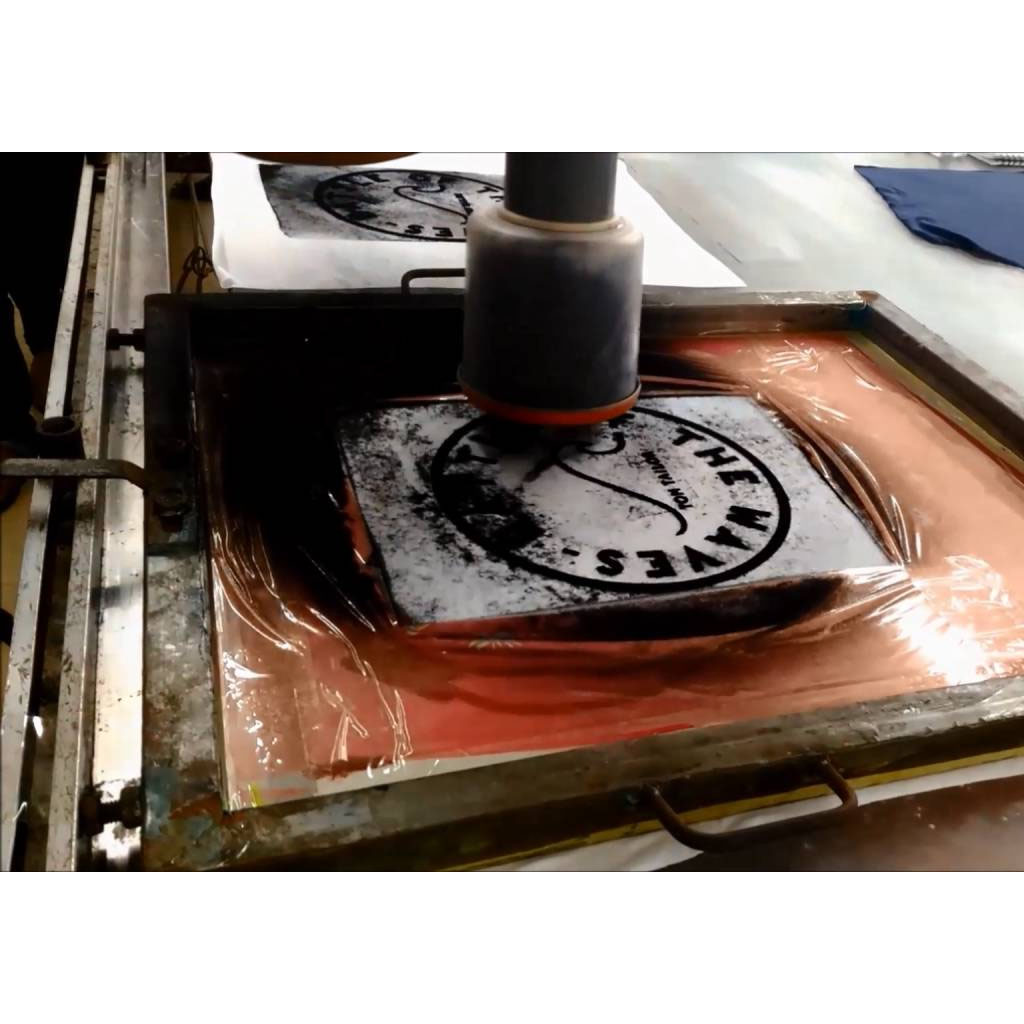
Screen Printing on Flock
Flock is composed comprised of synthetic fibres including cotton, rayon, and polyester. First, an adhesive liquid is applied to the selected printed area to ensure that the flock adheres to it, and then the flock is applied to it. The velvety and smooth feel of flock screen printing is achieved. For different colours, the flock is first dyed in that colour before being applied on the adhesive coating using a screen. As a result, the print is feathery light and feels incredibly premium.
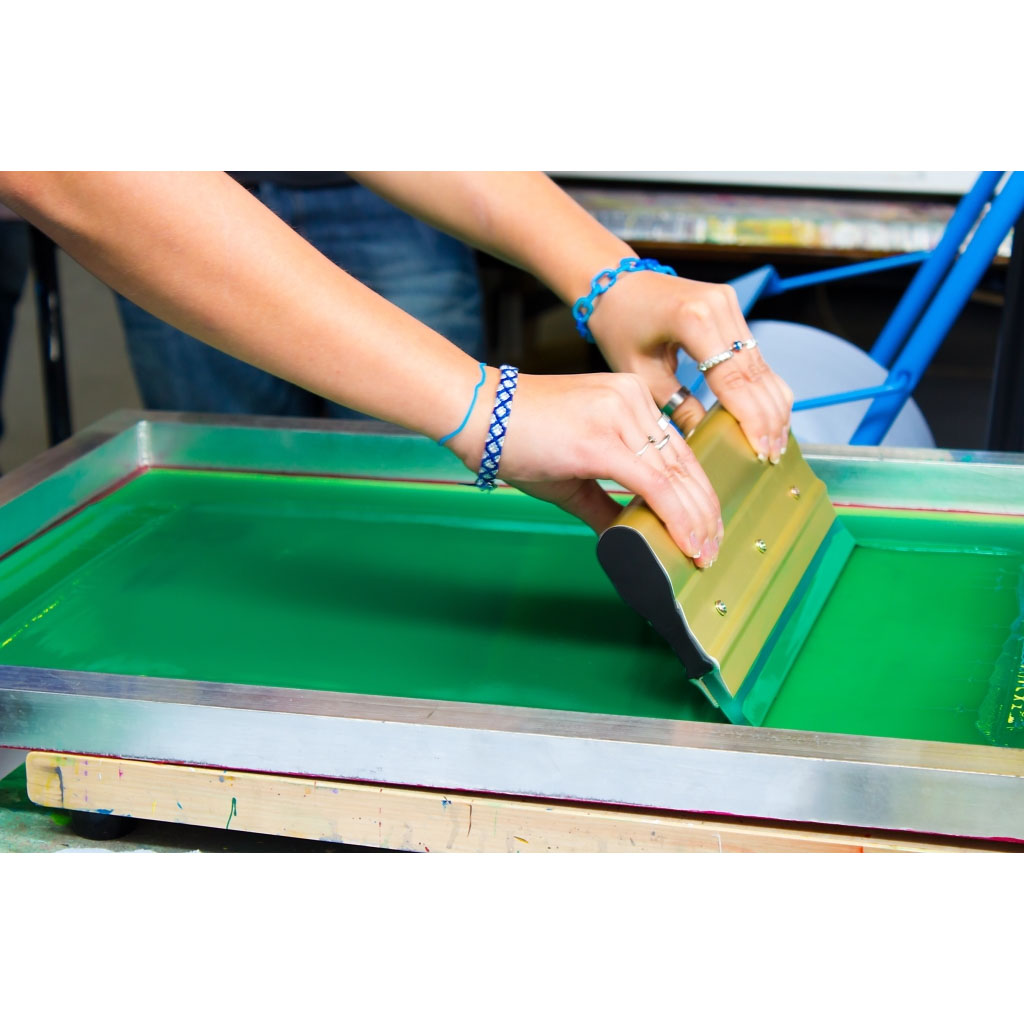
Screen Printing with Water/Pigment
Pigment screen printing, also known as water-based screen printing, is similar to discharge screen printing except that its pigment (colour) is based on water rather than a plastic-based liquid or Plastisol. It is typically used on white and light-colored clothing. Water-based printing is gentler to the touch and can be utilised with bright colours. Water-based screen printing produces the greatest results on light-colored fabrics such as white, off-white, or light grey, among others.
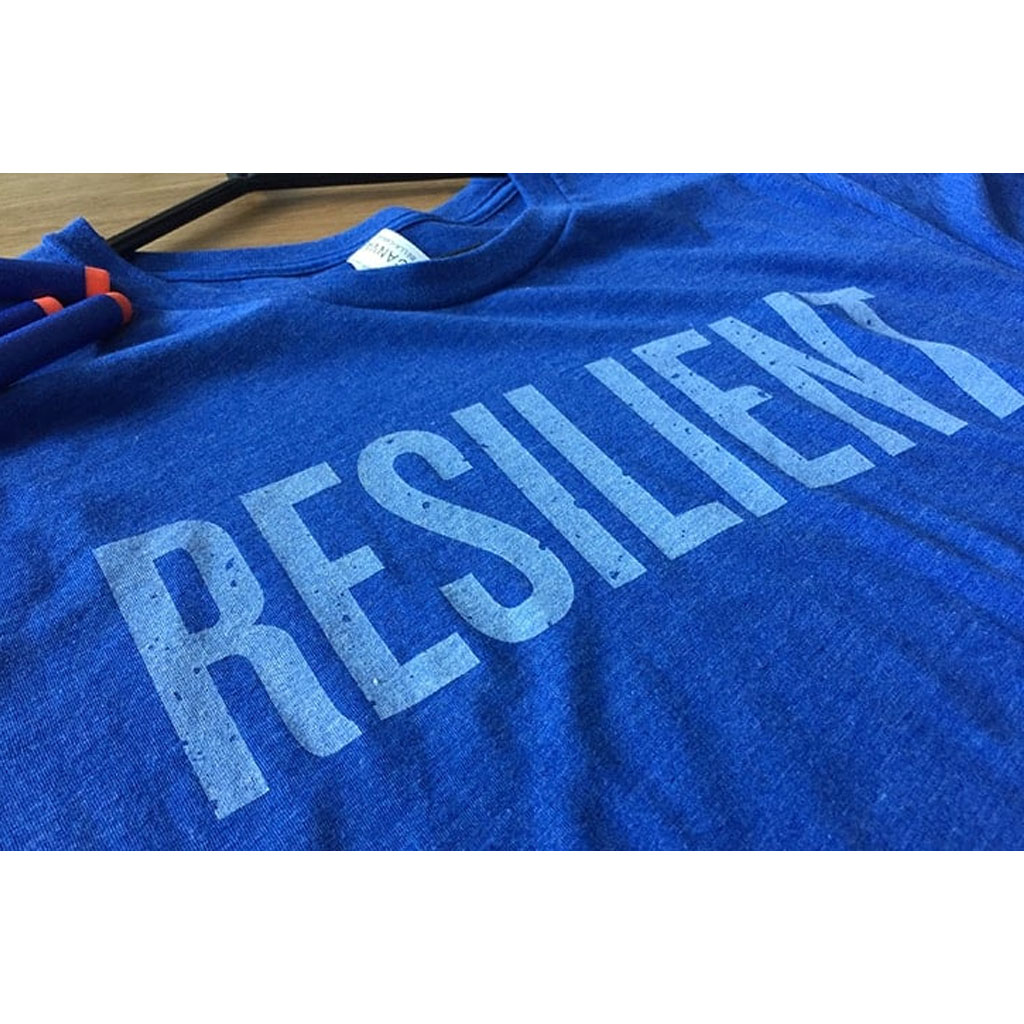
Printing on Discharge Screens
All of the same equipment is utilised for discharge screen printing, but the inks are different. For this type of printing, discharge inks are employed. When these inks are applied to shirts, they remove the original colour and replace it with the applied colour. Because the colour blends with the fabric, it has the appearance of basic cotton when touched. Discharge ink can be used as a stand-alone print or as an under foundation for other prints. It’s similar to a water-based printing alternative that can only be done in lighter colours.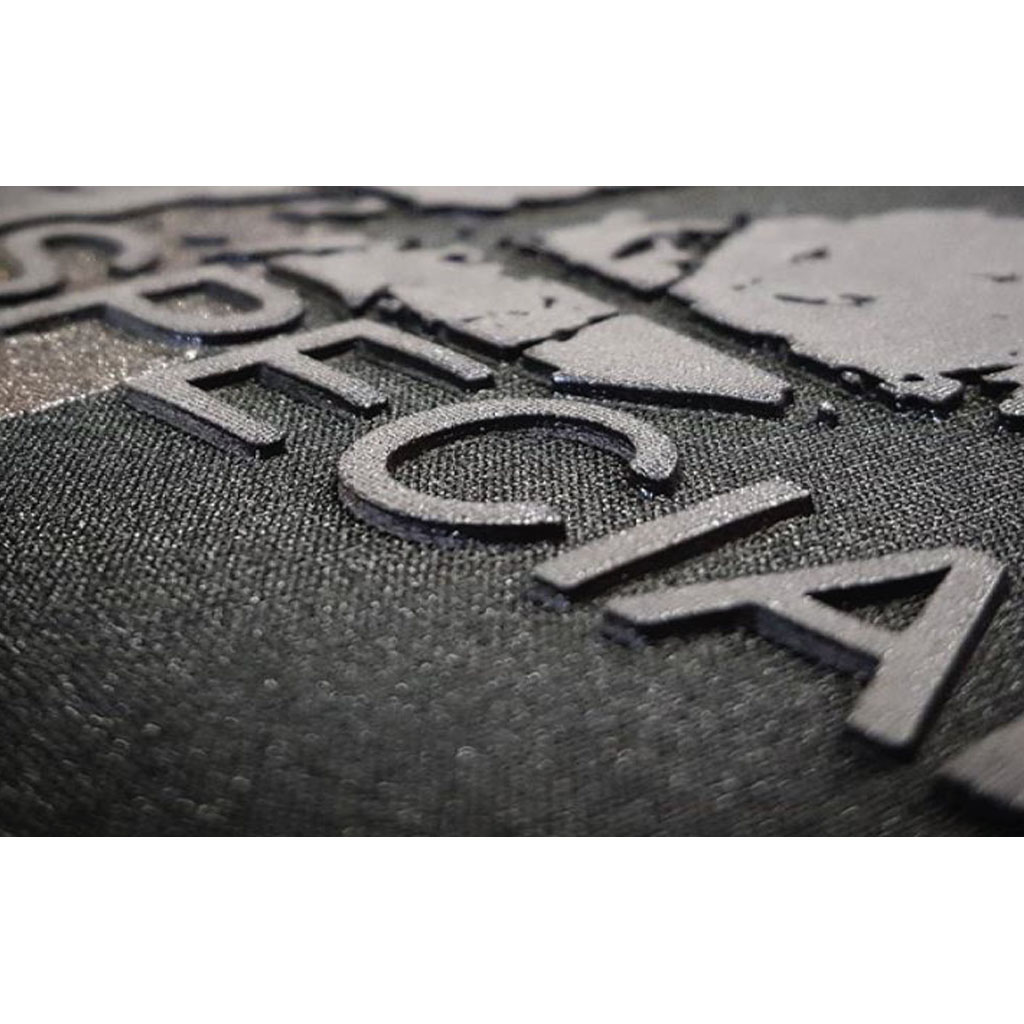
Printing with a High Density (3D)
High-density printing may appear to be high-quality puff printing at times, but it is not. Typically, puff printing lacks a distinct edge. Here is where high-density printing comes into play. Because high-density printing inks are very viscous, they do not adhere to screens. They simply pass through. That is why they have sharper and finer edges, but with a little extra puff, it also gives a 3D impression. It is not recommended to wash high-density prints on a regular basis since, unlike other printing technologies, they fade quickly. However, it could be quite useful if you want to place them on items that aren’t laundered on a regular basis.
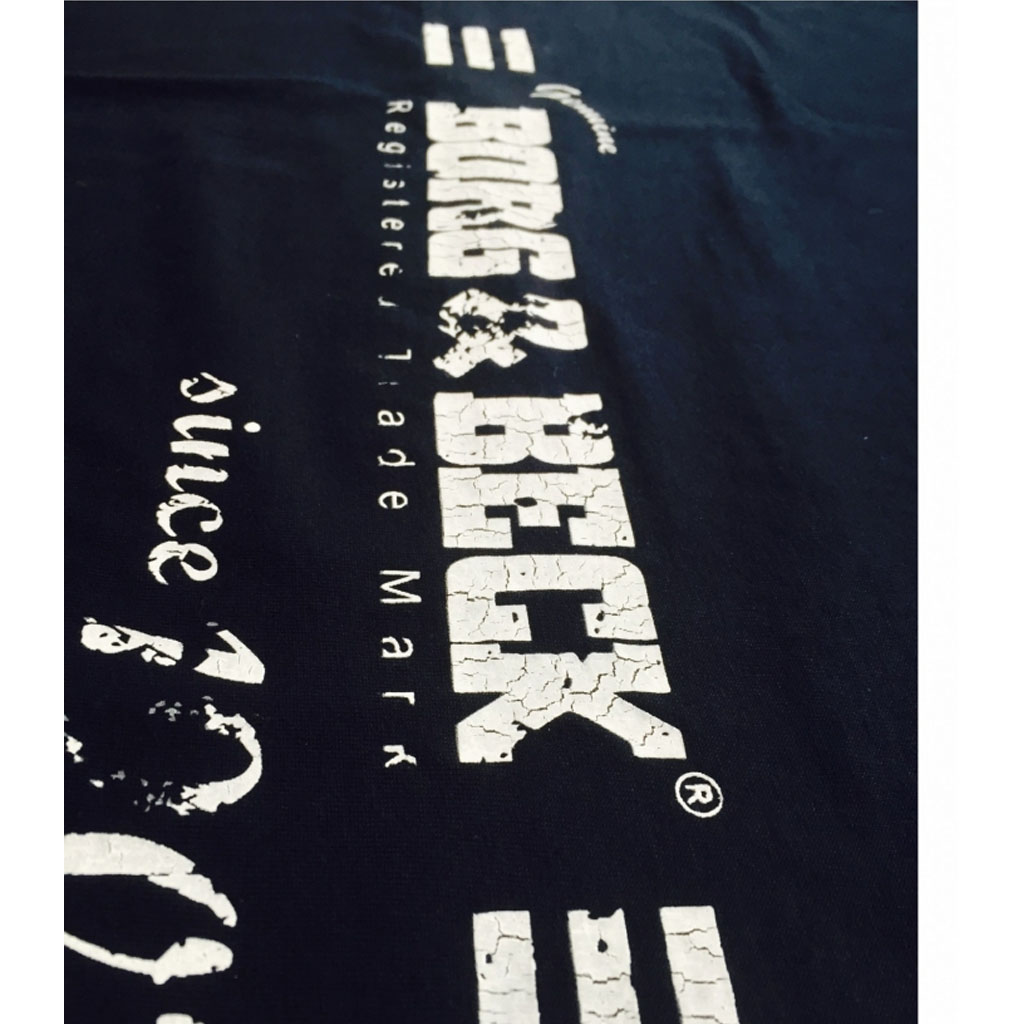
Screen Printing Crack
Shatter screen printing and distress screen printing are other terms for crack screen printing. A specific type of ink is utilised for the crack screen printing technique, which when dried produces a broken or shattered picture as desired by the clients. After adding cracking ink to the screens for transferring onto shirts, it is then dried with heat. When it dries, all of the cracks appear, giving it a broken appearance. It is used to give t-shirts, sweatshirts, and jackets a vintage look. Crack Screen Print helps your apparel business stand out from the crowd by making it unique.
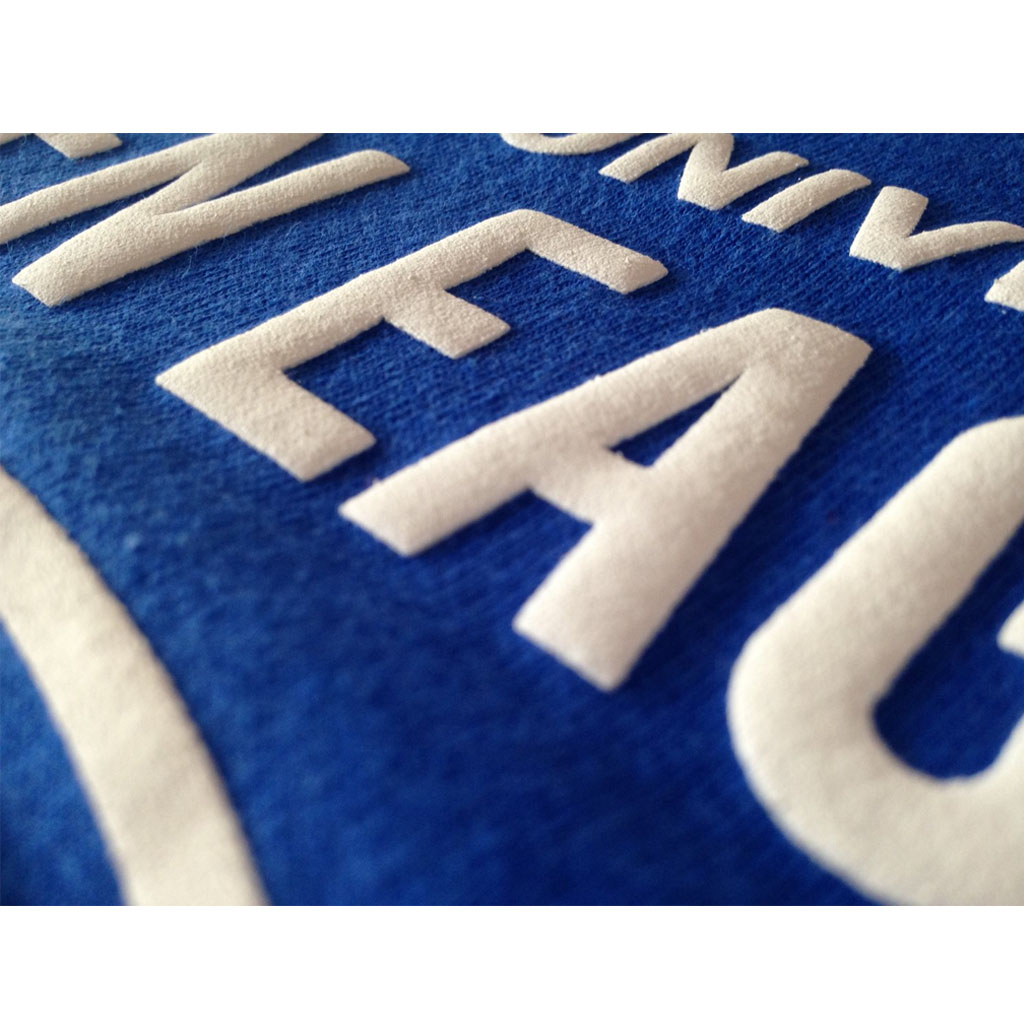
Screen Printing on Puff
Specialised puff inks are used in the puff screen printing process. This technique is quite popular and is currently utilised to give t-shirts, sweatshirts, or jackets a vintage look. However, it is sometimes utilised as part of a picture to draw attention to a single area or design inside a larger design. On screens, specialised puff printing ink is used for The Puff printing technique. Following the transfer of sufficient ink, a degree of heat is applied to the image to achieve the desired puff outcome. Some photos require pure puffs, while others require Plastisol as an addition to add shine and improve look. Puff screen printing is popular, although it is actually a puff with primarily air in between. As a result, the larger the puff, the more likely the print would shatter.
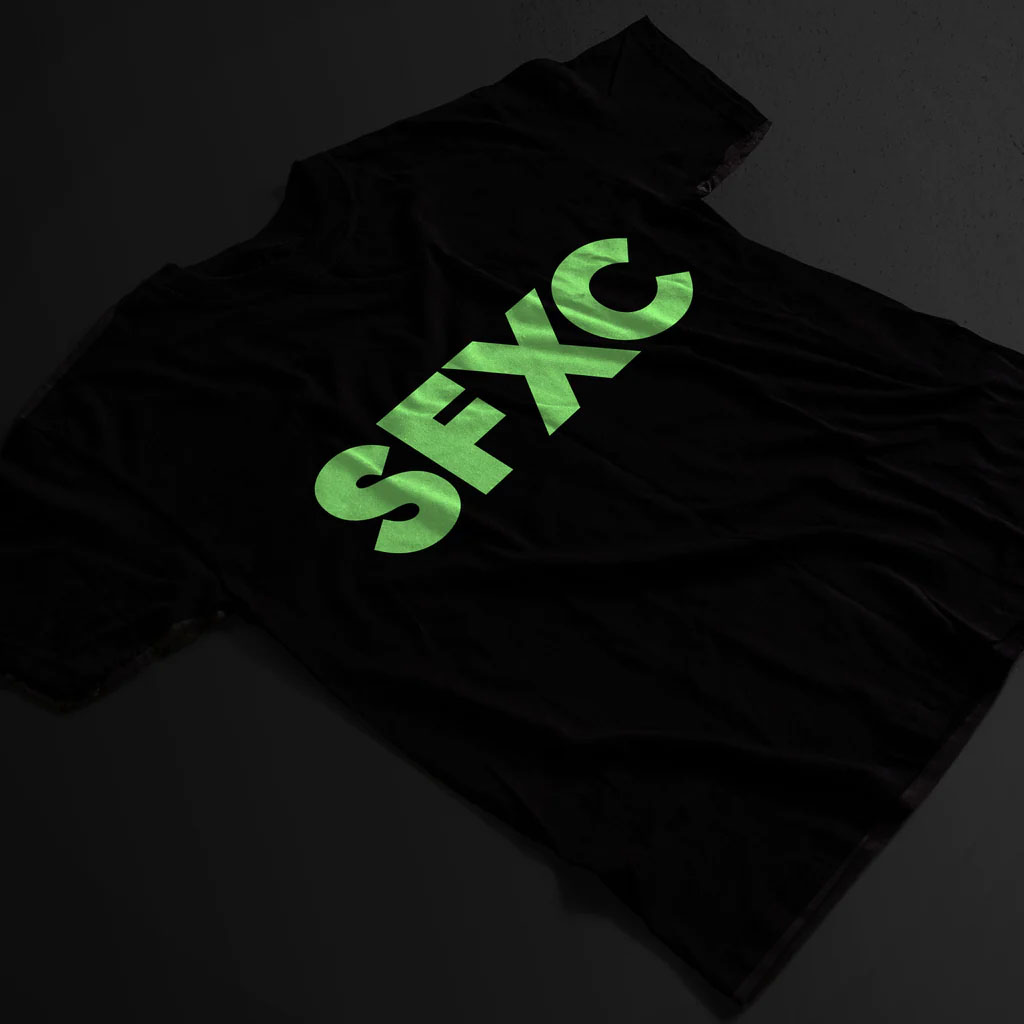
Printing that glows in the dark
This printing procedure is the same for glow-in-the-dark printing. The only difference is that the ink is Glow in the Dark. For the glow in the dark printing procedure, specialised neon inks are utilised. This ink is typically used to highlight images. This type of glow-in-the-dark printing image produces better results on darker-textured materials. These approaches are used to create quirky and interesting visuals that make a fashion statement. The shirt’s glow is only highlighted at night when it’s completely dark or in a room with no light. If you want to build a theme-based clothing line, it can also be used for Halloween costumes.
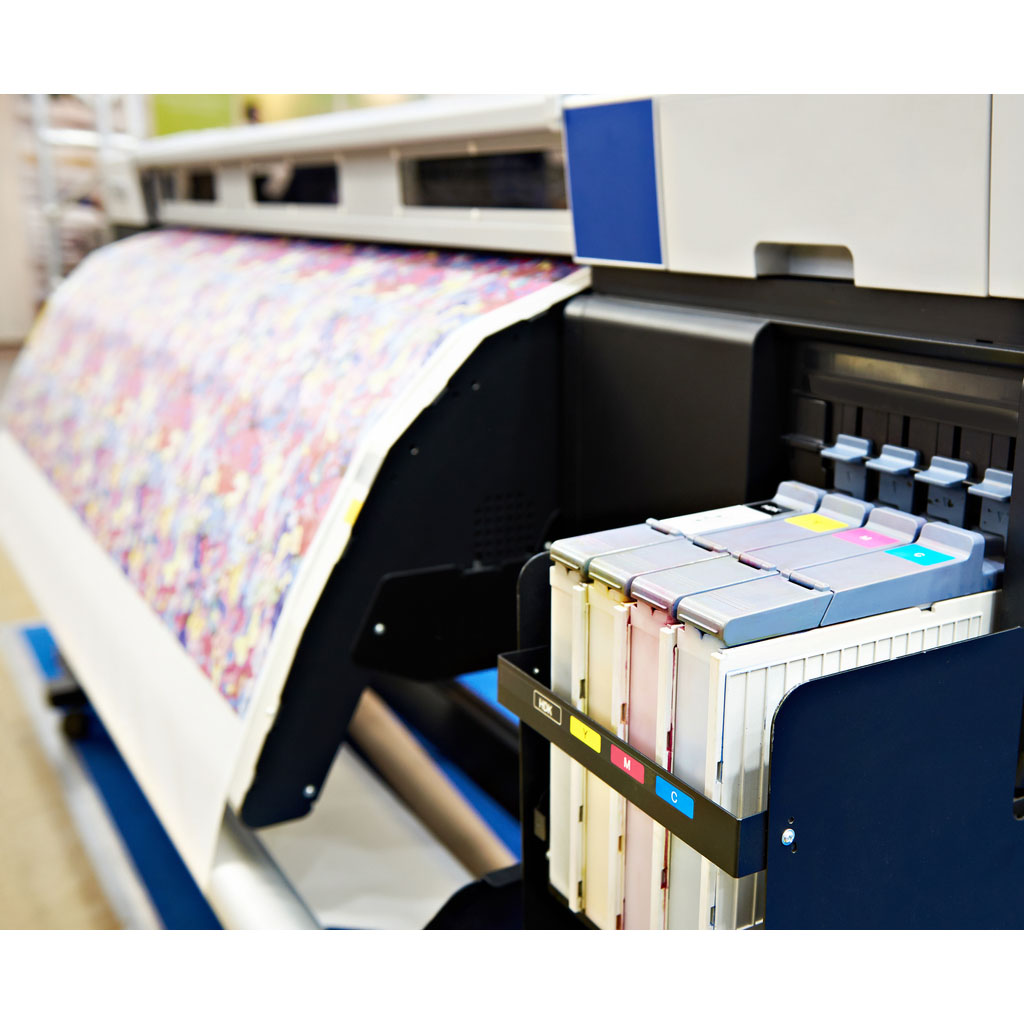
Process of Dye Sublimation
Sublimation printing is a more involved technique than heat transfers. Sublimation ink is applied to the desired region, then heat is applied. Because of the heat, this ink turns into a gas and then embeds onto the fabric, giving it a cleaner and more professional appearance. However, this procedure is only applicable to 100% polyester fabrics or polyester coating. This also necessitates the use of a heat press, however it should not be mistaken with heat transfer printing. Movemad International does not guarantee white spots on its sublimation printing because it prints on cut panels and then stitches them together for a more premium look. This method is also recommended for sports jerseys, which typically contain digital patterns and are constructed of moisture-wicking polyester cloth. To meet its objective, sublimation is normally done all over the shirt or any product, however Movemad International offers prints in any location as long as the polyester is white.
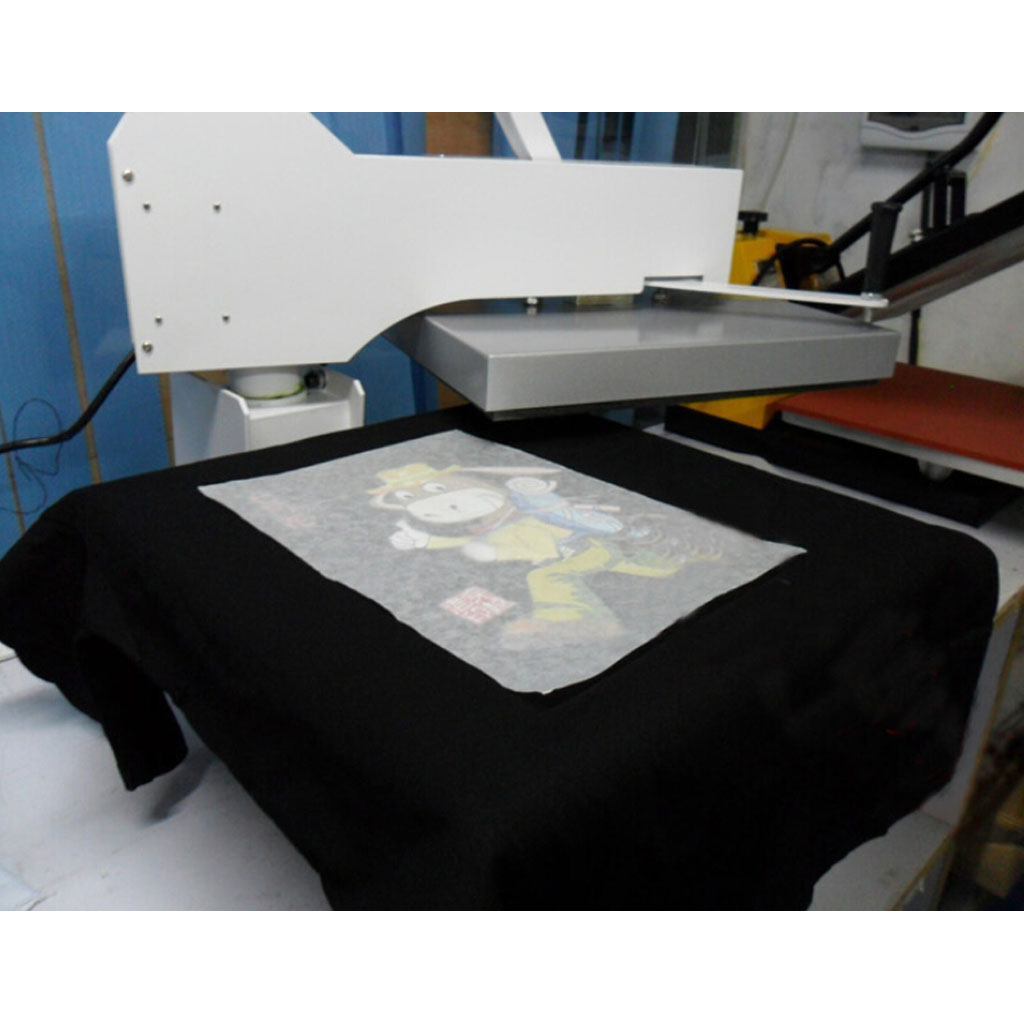
Printing on Stickers Using Heat Transfer
The heat transfer printing method is a simple and widely used approach. An picture is put onto paper and then ironed on the T-shirt to transfer the image, or in our case, a big industrial iron is used to transfer the images accurately, efficiently, and rapidly. This procedure necessitates a significant amount of heat application via those irons in order for the image to transfer from paper to the desired cloth. Because this is a simple technique, practically any image can be copied to the T-shirts. Because of the sticker nature of this printing, its endurance is unclear and it is not suggested for high-quality products.

Printing on Demand
Movemad International provides an alternative to sticker heat transfer printing that is significantly more reliable and has a lower rate of removal than heat transfer printing. The end effect is akin to a sticker being pasted on top of a garment, but it is far more durable and may be used to print real-life images onto the products.
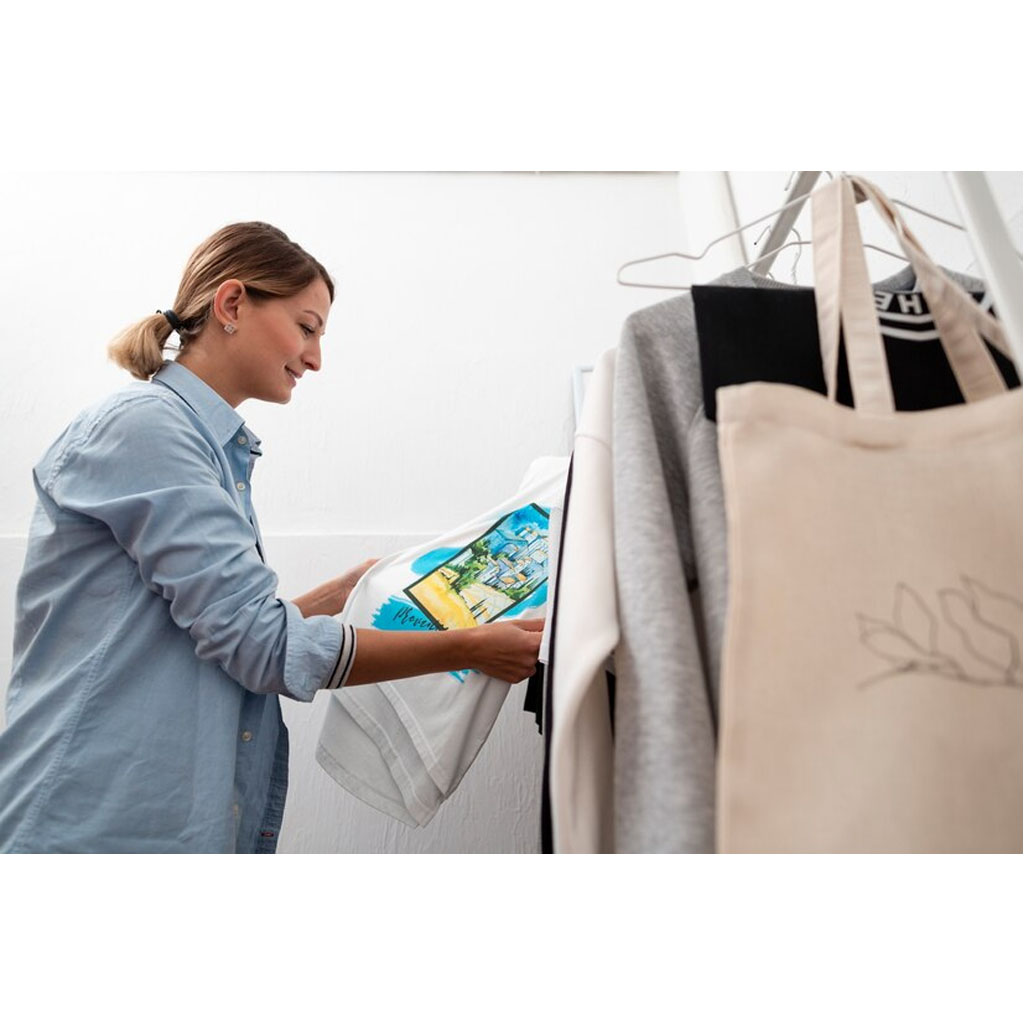
DTG stands for Direct to Garment.
DTG is one of the best and easiest methods to apply a print, but it has a higher minimum requirement due to its industrial use and expensive cost. Movemad International, on the other hand, offers this for the lowest minimum of 100 pieces and guarantees the print to be of the highest and feel-free quality. Any bespoke clothing company that offers Direct to Garment printing to its customers may undoubtedly propel your clothes brand to new heights, and Movemad International plans to achieve just that.